Factors to Consider When Selecting Brass Material for Electrical Components
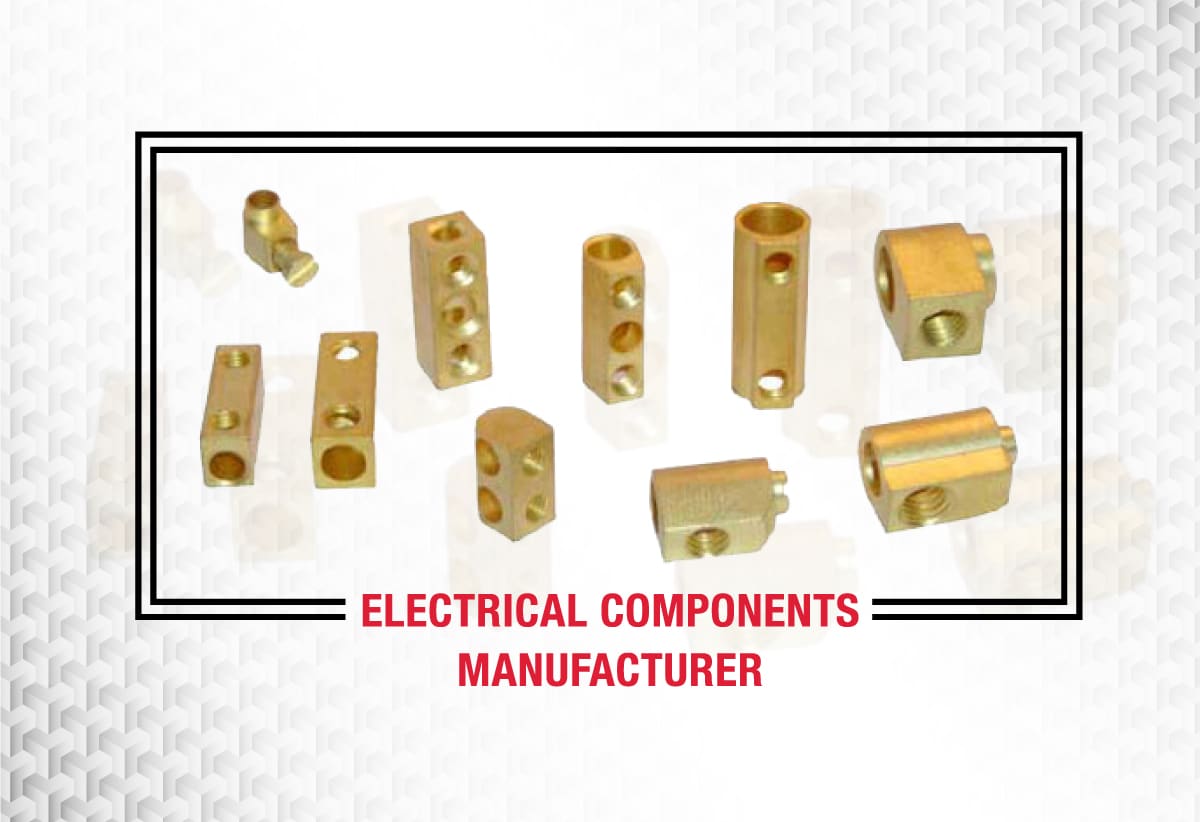
Brass is an alloy composed of copper and zinc and is known for its corrosion resistance, hardness, thermal conductivity, strength, and workability. It is a non-magnetic alloy with low friction and a variety of colours ranging from deep red to golden yellow. By adjusting the copper and zinc content, different mechanical and electrical properties can be achieved. It is possible to produce various kinds of brass by altering the copper-zinc ratio. Brass is used in a wide range of industries because of its different grades.
Choosing brass for electric components might be a bit difficult. Since there are various grades of brass, you need to consider which of these brass grades’ characteristics are a fit for your electric components. In this blog post, we’ll take a closer look at the various brass grades and factors to choose the right one that is commonly used for electric components.
Types of Brass Grades for Electrical Components
Brass is classified into different grades based on the amount of copper and zinc it contains. Different grades of brass also have different properties due to their variation in composition. We will review some of them here along with their advantages, disadvantages, and applications. Following are some factors that you might want to consider:
1. Brass C360
This alloy is commonly referred to as free-machining brass by manufacturer of electrical components. It is the most common brass grade used in machining. It is known for its high machinability and tensile strength. Due to its high lead content, which makes up about 3% of its composition, it is highly machinable.
Advantages
- Easily machinable.
- Corrosion resistance.
- Good tensile strength.
Disadvantages
- If lead content is used in medical applications, it could cause issues.
- Susceptible to acids.
2. Brass C230
Many metal component manufacturers refer to this brass grade as red or Nordic brass. Brass C230 has moderate strength but is significantly stronger than yellow brass and has highly effective anti-rust properties. It is the most preferred brass type because of its ability to resist dezincification and seasoning. Manufacturers also use it for making pipe service lines due to its resistance to water corrosion. It is ideal for custom brass components, parts, or products.
Advantages
- Resistance to dezincification.
- Moderate tensile strength.
- Easily cold worked, hot formed, soldered, and brazed.
- Most durable for commercial and industrial.
Disadvantages
- In harsh environments, it might not be able to withstand corrosion.
3. Brass C220
Manufacturers of industrial electrical components refer to this alloy as commercial bronze. The higher copper content still makes it a brass alloy despite its name. It has a high machinability rating, strength, and flexibility. It is a favourite in the architectural world and is used to manufacture weather stripping.
Advantages
- Excellent corrosion resistance.
- Good machinability rating.
- High capacity for being cold worked.
Disadvantages
- The material might need to be annealed more after exposure to harsh conditions.
4. Brass C300
Brass grades C300 to C30000, which are also known as intermediate brasses or alpha-beta brasses, have a balance of copper and zinc. Their attributes make them suitable for a variety of applications across various industries, providing them with a comprehensive set of attributes.
Advantages
- Balance between strength and ductility.
- Easily shaped and formed.
- Exhibit good corrosion resistance.
- Offer good machinability.
Disadvantages
- Expensive compared to other grades.
- Regular maintenance requires.
Machining Time of Electrical Components
It is important to consider the lead times for different projects when determining which brass grade to use. For electrical components, the C360 is the most suitable brass grade in terms of machinability. So, if you need custom brass electrical components urgently, the C360 is an overwhelming material favourite. However, if you require other properties apart from machinability, you could assess other grades like the C230 or the C220.
Electrical Component Design
You should ensure your parts design is not too complex for machining, even though brass grades are quite easy to machine. Furthermore, it is recommended to minimize the number of machine setups. In this way, the machining cost of the project can be reduced.
Application of Electrical Components
There are various strengths and weaknesses to each brass grade because of their different compositions. Depending on how you plan to use the component, the brass will be suitable for electrical components. If you decide that brass is the right metal for your electrical component, you should make sure that its applications match the brass grade’s property profile.
Brass is an incredibly versatile material that can be used in a wide variety of applications due to its durability, malleability, strength, and corrosion resistance properties. There are several types of brass alloy compositions available on the market today, each offering unique characteristics suited for specific tasks depending on the desired outcome. Whether you’re looking for a material with superior machinability or one with excellent wear resistance – there is sure to be a brass alloy out there that meets your needs! For engineers and materials scientists who work with brass alloys regularly – understanding these different compositions can help inform their decisions when selecting the best option for your electrical component requirements.
Considering all the factors discussed above will help you make the right decision to choose brass grade for high-quality electrical components. And still, if you are not sure, or just want to talk through your requirements. Our team of experts can simplify the manufacturing process for you, helping to select the right brass grade for electrical components. To learn more about our services and offered range of brass components, contact us at info@brasscomponent.co.uk or request a quick quote!